Development of the modeling and control methods for reconfigurable cable robots taking into account elastic deformations of mechanical elements
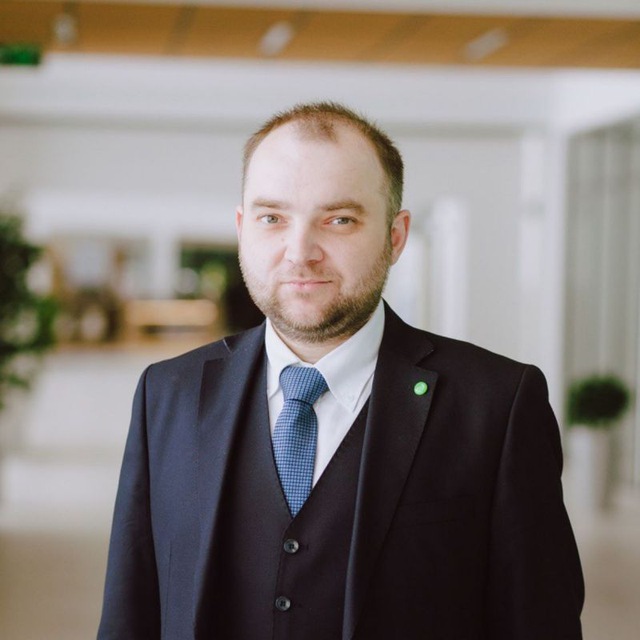
Alexandr Klimchick
project lead
Partners: | ARKODIM-Pro LLC |
Laboratory: | Laboratory of mechatronics, control and prototyping |
Status: | Завершен |
The aim of the project is to develop the theory of manipulators of the parallel structure as applied to manipulators in which the movement of the working body is controlled by flexible connections - cable robots.
A cable or cable robot is a mechanical system in which a working body is suspended on several cables. The control of the movement of the working body is due to the coordinated operation of the engines providing winding or etching of the cables. In contrast to traditional handling equipment in a cable robot, the position of the working body is directly controlled with the help of cables, and it is possible to control the orientation of the working body in space to some extent.
The ability to control the position and orientation of the working body with high accuracy and at significant speeds determines the main advantages of cable robots. Cable robots are used in television and film shooting in stadiums, for assembling or painting large-sized products, 3D printing of large objects, in motion simulators, in the development of exoskeletons for rehabilitation. Among scientific tasks, it should be noted the development of methods for mathematical modeling of kinematics and dynamics taking into account elastic deformations of mechanical elements of the robot, methods, and algorithms for parametric calibration, methods of optimal motion control taking into account deformations of mechanical elements and manufacturing errors of actuating drives and transmissions, methods for the operative diagnosis of possible malfunctions and defects in cable robots. The prototype of a cable robot developed at Innopolis University is a modular reconfigurable system that allows the installation of 4 to 12 cables, for which Omron servos and servomotors are used.
The dimensions of the working area of the robot are 9x4x3 m, the carrying capacity of the robot is up to 200 kg, the maximum speed of the working body with a load of up to 0.5 m / s. The prototype is designed to conduct research and development of developed methods and control algorithms.